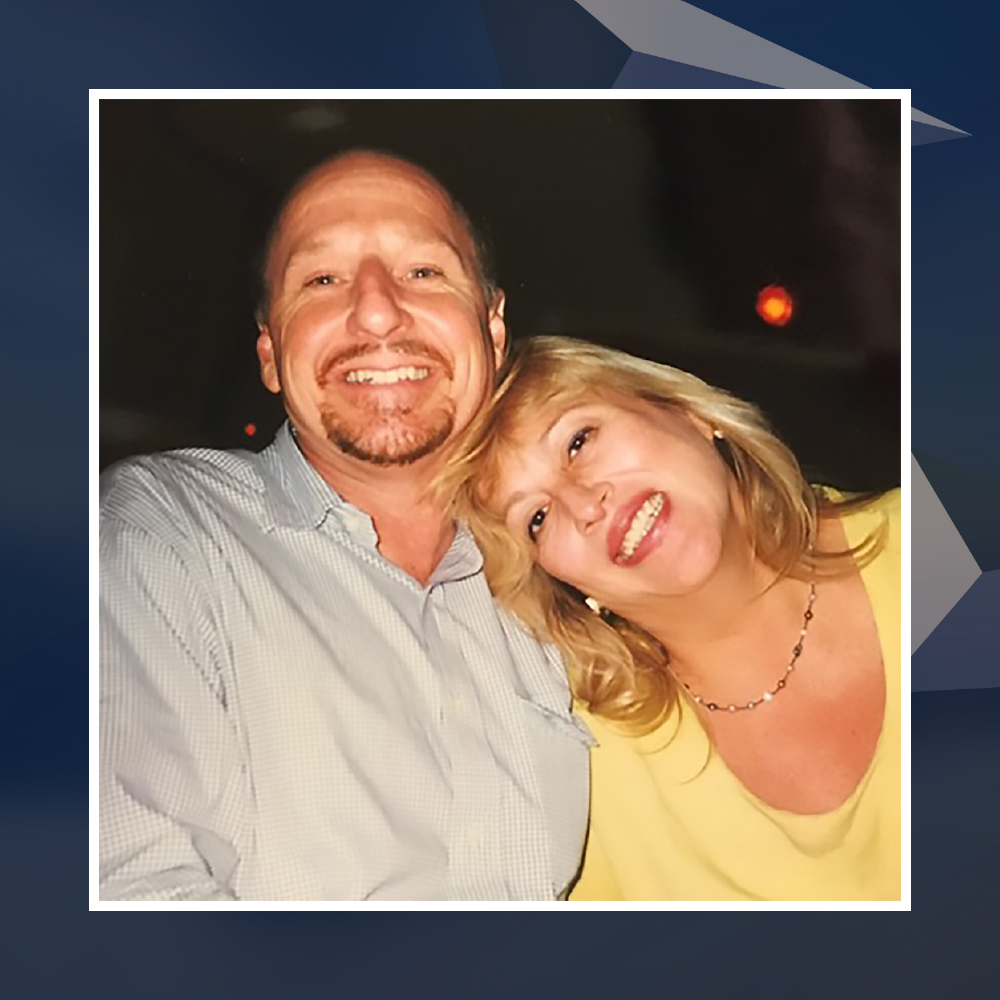
Sand control plays a crucial role in the oil and gas industry, ensuring the uninterrupted flow of hydrocarbons while minimizing equipment wear and preventing wellbore damage. Innovations in screen product manufacturing are now transforming how companies approach sand control. The focus has shifted toward creating screens with higher durability, greater precision in sand particle filtration, and enhanced adaptability for complex, healthy conditions. Advanced computational models now aid in designing screens tailored to specific reservoirs, ensuring that manufacturers can anticipate potential challenges and address them early in the production process. These technologies also enhance the longevity of screens, reducing downtime and improving operational efficiency.
The Rise of Smart Screens and IoT Integration
The future of sand control is being shaped by the integration of intelligent technology and the Internet of Things (IoT). Modern screens are being developed with embedded sensors that monitor well conditions in real time. These sensors can detect changes in pressure, flow rates, and sand influx, providing operators with valuable data to prevent issues before they arise. This trend toward predictive maintenance ensures timely interventions, minimizing costly repairs and downtime. Additionally, data collected from intelligent screens enhances decision-making, allowing companies to optimize production strategies and extend equipment life. IoT-enabled screens represent a shift from reactive to proactive sand control solutions, setting a new standard in product performance.
Sustainable Materials and Green Manufacturing Practices
Sustainability is becoming a core focus for manufacturers across industries, and sand control screen production is no exception. Companies are exploring new materials that are both environmentally friendly and capable of withstanding harsh good conditions. Recycled metals, biopolymers, and advanced coatings are now being used to create screens that are durable yet sustainable. Moreover, green manufacturing practices, such as reducing energy consumption and minimizing waste, are gaining traction in screen production facilities. These efforts not only reduce the environmental impact but also align with the industry’s goal of achieving net-zero carbon emissions. As regulations around sustainability tighten, manufacturers that adopt green practices will likely gain a competitive edge.
Customization and Modular Screen Designs
Another significant trend in screen product manufacturing is the move toward customization and modularity. No two oil fields are alike, and operators are demanding screens that can be tailored to specific reservoir conditions. Modular designs allow operators to adjust screen configurations on-site, providing flexibility to adapt to changing healthy conditions without needing to replace the entire screen. This approach reduces costs and improves operational efficiency, particularly in offshore and deepwater environments where logistical challenges are shared. Customization is also becoming more precise, with manufacturers leveraging 3D printing technology to create screens with intricate designs that enhance sand filtration capabilities.
Automation and Robotics in Manufacturing
Automation and robotics are reshaping how screens are manufactured, significantly improving productivity and product quality. Automated systems enable manufacturers to produce screens with high precision and consistency, reducing the risk of defects. Robotics play a pivotal role in assembling complex screen components, ensuring tighter tolerances and enhanced durability. These technologies not only streamline production but also improve workplace safety by minimizing human exposure to hazardous conditions. As the demand for efficient manufacturing increases, companies are investing in automated production lines that can scale operations while maintaining strict quality standards.
The Impact of Artificial Intelligence on Quality Control
Artificial Intelligence (AI) is revolutionizing quality control in screen product manufacturing. AI-powered systems can analyze vast amounts of production data in real-time, identifying anomalies and defects that might otherwise go unnoticed. Machine learning algorithms also predict potential failure points, enabling manufacturers to take corrective actions early in the process. This ensures that only the highest quality screens reach the market, reducing the likelihood of field failures. In addition, AI enhances the testing and validation process, helping manufacturers develop more reliable products that meet the evolving needs of the oil and gas industry.
The Shift Toward Collaborative Industry Partnerships
Collaboration is becoming a key strategy in the future of sand control screen manufacturing. Manufacturers are forming partnerships with oilfield service companies, research institutions, and technology providers to drive innovation. These collaborations facilitate knowledge-sharing and accelerate the development of new screen technologies. By working closely with industry stakeholders, manufacturers gain insights into emerging challenges and can co-develop solutions that address them effectively. This trend toward collaboration also extends to the digital space, with companies forming data-sharing alliances to improve predictive maintenance and optimize screen performance.
A Future of Innovation and Sustainability
A convergence of technological innovation, sustainability, and collaborative partnerships is shaping the future of sand control screen manufacturing. Bright screens equipped with IoT capabilities are transforming how operators monitor well conditions, while sustainable materials and green manufacturing practices are reducing the industry’s environmental footprint. Customization, automation, and AI-driven quality control are further enhancing product performance and reliability. As the oil and gas industry continues to evolve, manufacturers that embrace these trends will be well-positioned to meet future demands, ensuring efficient operations and long-term success. The journey toward more innovative, adaptable, and sustainable sand control solutions has only just begun, promising a future full of opportunities for those prepared to lead the way.