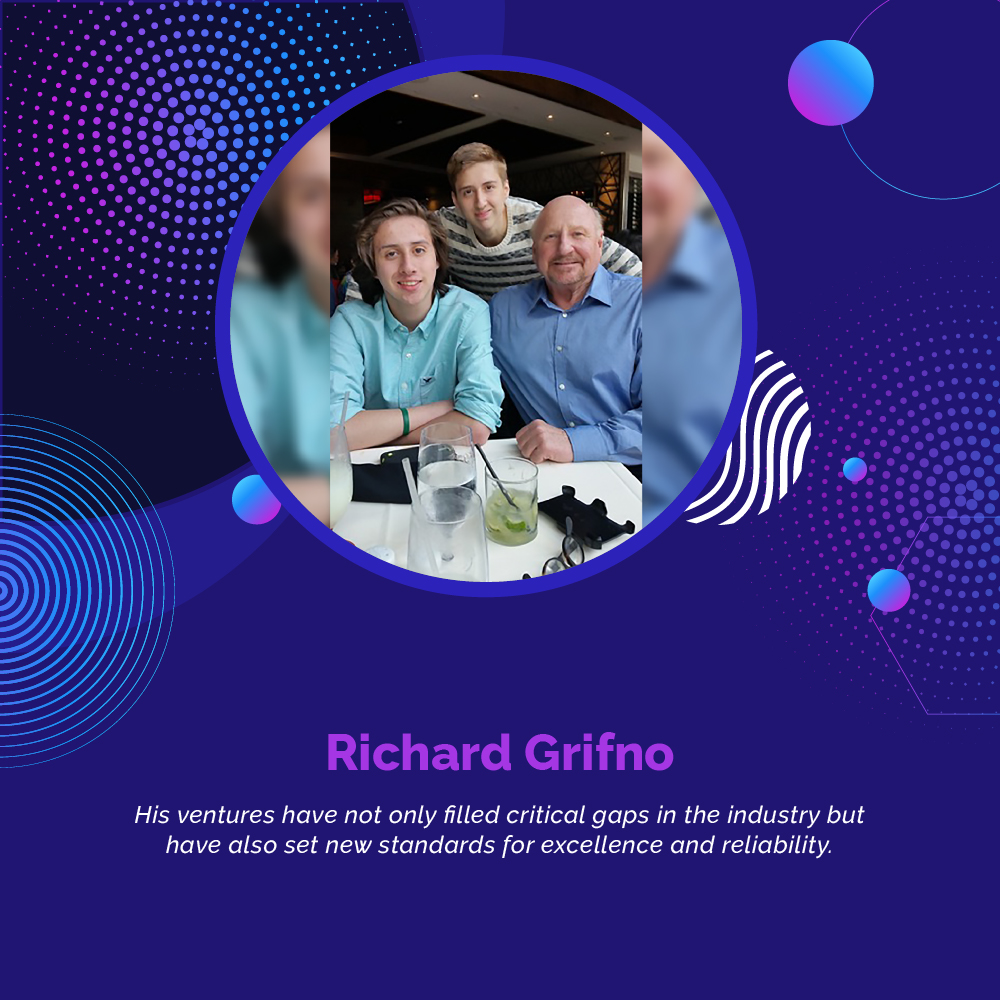
The oil and gas industry is one of the most critical sectors in the global economy, and screen manufacturing plays a vital role in extraction and production. These screens are essential components used in various filtration and separation processes, ensuring efficient and effective oil and gas extraction. However, like many specialized manufacturing industries, oil and gas screen manufacturing faces several significant challenges that must be addressed to maintain operational efficiency, product quality, and cost-effectiveness.
Material Durability and Corrosion Resistance
One of the foremost challenges in oil and gas screen manufacturing is the need for materials that can withstand the harsh operating environments typical of oil and gas exploration and production. These screens are often exposed to extreme pressures, temperatures, and corrosive substances. The materials used in their construction must have exceptional durability and corrosion resistance to maintain performance over extended periods.
Corrosion, in particular, is a major issue in offshore and onshore drilling environments, where exposure to saltwater, high humidity, and chemicals can quickly degrade traditional materials. Manufacturers must continually research and develop new alloys and composite materials that resist these conditions. However, finding the perfect balance between durability and cost-efficiency remains difficult, as more resistant materials tend to be expensive.
Maintaining Precision in Screen Design and Manufacturing
Oil and gas screens need to be manufactured with high levels of precision to perform effectively in separation and filtration processes. Even minor imperfections in the mesh size or screen alignment can result in inefficient filtration, leading to significant operational problems, including equipment damage and costly downtime.
Achieving this level of precision in screen manufacturing is challenging due to the complexity of the designs and the materials used. Advanced manufacturing techniques, such as laser cutting and computer-aided design (CAD), are often required to meet these exacting standards. However, adopting these technologies involves significant investment in machinery and workforce training, which can be a barrier for some manufacturers.
Adapting to Changing Industry Standards and Regulations
The oil and gas industry is highly regulated, with stringent environmental and safety standards to minimize the impact of drilling and extraction activities. These regulations constantly evolve; manufacturers must adapt their products and processes to remain compliant. For oil and gas screen manufacturers, this often means redesigning products to meet new requirements, which can be costly and time-consuming.
For example, regulations around using certain materials or managing waste products during the manufacturing process may change, requiring manufacturers to invest in new technologies or alter their production methods. Failure to comply with these regulations can result in fines, delays, or even bans on selling products in certain markets, which makes staying ahead of regulatory changes essential for manufacturers.
The Need for Customization in Screen Design
The oil and gas industry’s diverse needs mean that screen manufacturers must offer a wide range of products tailored to specific applications. Screens used in deep-sea drilling, for instance, may have vastly different requirements than those used in shale gas extraction. This level of customization adds complexity to the manufacturing process, as manufacturers must be able to quickly adjust their production lines to accommodate different designs, sizes, and materials.
Customization can also lead to longer lead times and higher production costs, as manufacturers may need to produce small batches of highly specialized products. Balancing the need for customization with the demand for cost-effective, scalable production is a major challenge in the industry.
Ensuring Product Consistency and Quality Control
Consistency in the quality of screens is critical in oil and gas operations, as any deviation can result in operational failures. Quality control processes must be stringent to ensure that every screen meets the specifications and can perform reliably in the field. This involves thorough testing at multiple stages of production, from the selection of raw materials to the final inspection of finished products.
However, implementing and maintaining these quality control measures can be resource-intensive. Manufacturers must invest in sophisticated testing equipment and develop robust quality assurance protocols to identify and rectify defects before products are shipped to customers. In addition, skilled workers are required to oversee these processes, adding to the overall cost of production.
Technological Advancements and Innovation Pressure
The oil and gas industry constantly evolves, with new technologies and methods being developed to improve efficiency and reduce environmental impact. This creates pressure on screen manufacturers to innovate and keep pace with the industry’s changing demands. For example, hydraulic fracturing (fracking) has increased demand for screens that can handle higher pressures and more abrasive materials.
Manufacturers that fail to invest in research and development risk falling behind their competitors as customers increasingly seek innovative solutions that provide better performance and longer service life. However, developing new products is not challenging, as it requires significant investment in time and resources.
Supply Chain Disruptions and Raw Material Availability
Another challenge oil and gas screen manufacturers face is the volatility of the global supply chain. The industry relies on a steady supply of high-quality raw materials, such as metals and specialized alloys, to produce screens that meet industry standards. However, fluctuations in the availability and cost of these materials can create significant disruptions in the manufacturing process.
Various factors, including geopolitical instability, natural disasters, and economic sanctions, can cause supply chain disruptions. Manufacturers must have contingency plans to mitigate these disruptions’ impact, such as sourcing alternative materials or diversifying their supplier base. However, this adds another layer of complexity and cost to the manufacturing process.
Oil and gas screen manufacturers face multifaceted challenges, ranging from material durability and regulatory compliance to the need for innovation and sustainability. Overcoming these obstacles requires combining advanced manufacturing techniques, strategic investment in research and development, and a commitment to quality and environmental responsibility. As the oil and gas industry evolves, screen manufacturers must adapt and innovate to stay competitive in this critical sector.