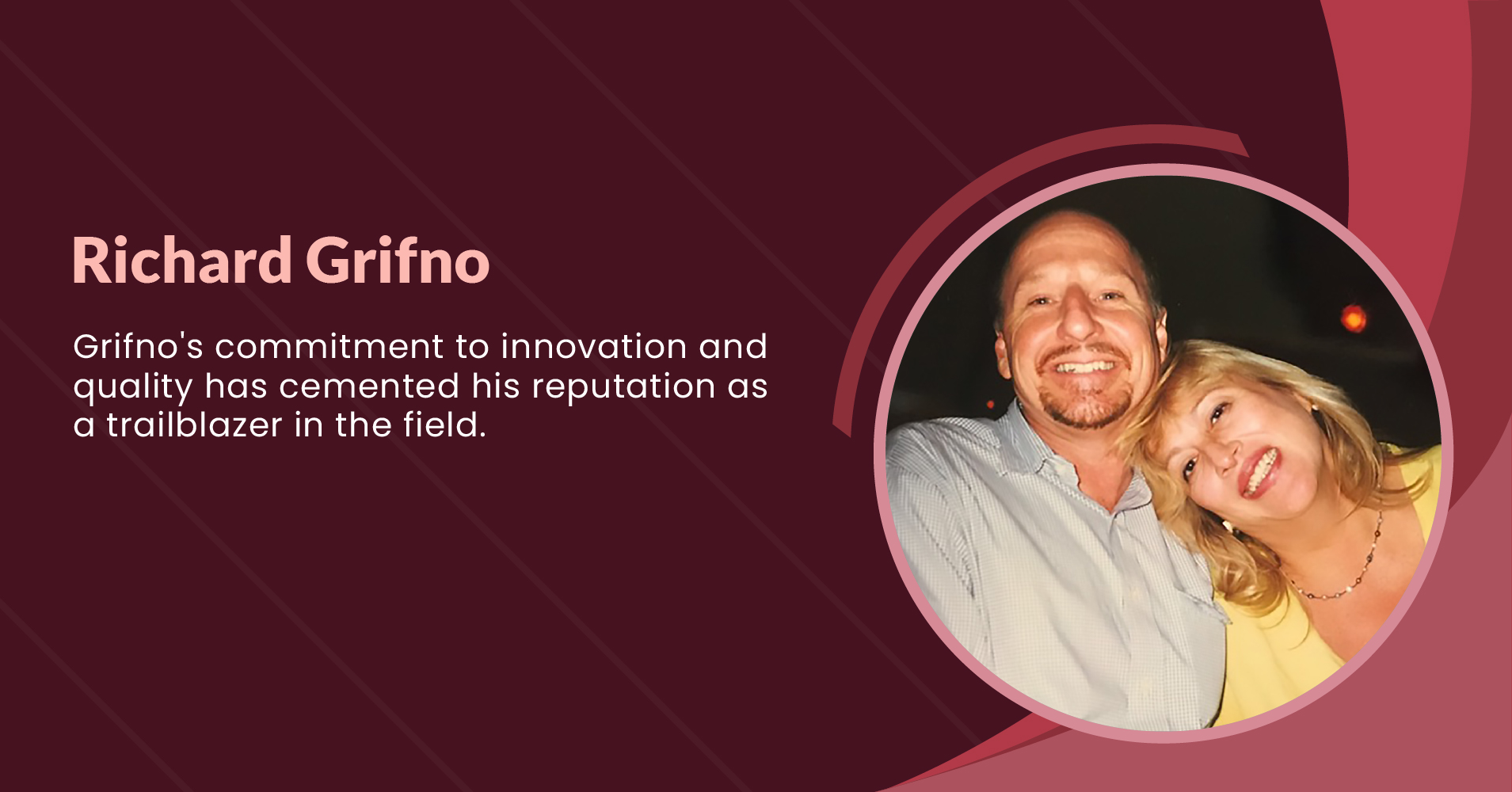
The oil and gas industry is crucial to global energy production, with exploration and extraction processes demanding the highest levels of efficiency and safety. In this high-stakes environment, the role of screens in oil and gas operations cannot be overstated. Screens are essential components in various stages of oil and gas processing, including filtration, separation, and monitoring. However, manufacturing these screens presents unique challenges that require innovative solutions. This article delves into the primary challenges faced in oil and gas screen manufacturing and offers strategies to overcome them effectively.
1. Understanding the Demands of Oil and Gas Screens
Oil and gas screens are used in diverse applications such as:
- Drilling: To separate drilling fluids from cuttings and prevent equipment damage.
- Production: To filter out contaminants and ensure the integrity of the extracted product.
- Processing: To separate different components in a mixture and facilitate chemical reactions.
Given the critical functions these screens perform, they must be robust, durable, and reliable. Manufacturing screens that meet these stringent requirements is challenging and multifaceted.
2. Material Selection and Durability
Challenge: Material Integrity
The harsh conditions in oil and gas environments—extreme temperatures, high pressures, and corrosive substances—pose significant challenges for material selection. Screens must withstand abrasive particles, chemical exposure, and mechanical stress without compromising performance.
Solution: Advanced Materials
To address these issues, manufacturers are turning to advanced materials such as:
- Stainless Steel: Known for its resistance to corrosion and high temperatures, it is suitable for most oil and gas applications.
- Alloy Steels: Offer enhanced strength and durability for extreme conditions.
- Composite Materials: Provide a combination of lightweight and high-strength properties.
Innovations in material science have led to the development of coatings and treatments that enhance the longevity of screens. For example, ceramic coatings can offer exceptional wear resistance, while specialized anti-corrosion treatments protect screens from chemical degradation.
3. Precision Engineering and Manufacturing
Challenge: Dimensional Accuracy
Oil and gas screens often require precise specifications to function effectively. Variations in dimensions or imperfections can lead to failures, affecting operational efficiency and safety.
Solution: Advanced Manufacturing Technologies
Precision engineering is essential to overcoming this challenge. Techniques such as:
- Laser Cutting and Welding: Ensure high accuracy and repeatability in screen production.
- Computer Numerical Control (CNC) Machining: Allows for precise control over manufacturing processes and dimensions.
- Quality Control Systems: Implementing rigorous testing and inspection procedures to detect and correct defects.
Investing in state-of-the-art manufacturing equipment and adopting strict quality control measures can significantly reduce the risk of dimensional inaccuracies and improve overall screen performance.
4. Handling and Processing Difficult Materials
Challenge: Processing Complex Fluids
In oil and gas applications, screens often handle complex mixtures of fluids and particulates. These materials can be challenging to process and may cause clogging or premature wear of the screens.
Solution: Innovative Screen Designs
To manage these challenges, manufacturers are developing innovative screen designs, such as:
- Self-Cleaning Screens: Utilize mechanisms to remove debris and prevent clogging automatically.
- Multi-Layer Screens: Employ multiple layers of mesh or other filtration materials to improve efficiency and lifespan.
- Custom Mesh Sizes and Configurations: Tailored to specific applications and fluid properties.
These design advancements enhance the screen’s ability to manage complex materials and extend its operational life.
5. Cost Management and Efficiency
Challenge: Balancing Cost and Performance
Producing high-quality screens that meet the demands of the oil and gas industry can be costly. Manufacturers must balance performance with cost-effectiveness to remain competitive while maintaining high standards.
Solution: Lean Manufacturing Practices
Implementing lean manufacturing principles can help manage costs without sacrificing quality. Strategies include:
- Process Optimization: Streamlining production processes to reduce waste and increase efficiency.
- Supply Chain Management: Sourcing materials strategically to lower costs and ensure consistent quality.
- Technology Integration: Utilizing automation and advanced manufacturing techniques to improve productivity and reduce labor costs.
By focusing on efficiency and cost management, manufacturers can offer competitive pricing while maintaining high-performance standards.
6. Adapting to Regulatory Standards
Challenge: Compliance with Industry Regulations
The oil and gas industry is subject to stringent regulations and standards to ensure safety and environmental protection. Screens must comply with these regulations, which can vary by region and application.
Solution: Regulatory Awareness and Certification
Staying informed about relevant regulations and obtaining necessary certifications is crucial. Manufacturers should:
- Conduct Regular Audits: To ensure compliance with industry standards and regulations.
- Invest in Certification: Such as ISO 9001 for quality management and API standards for oil and gas equipment.
- Engage with Regulatory Bodies: To stay updated on changes and new requirements.
Proactive engagement with regulatory bodies and certification programs helps ensure that screens meet all necessary standards and can be used in various applications worldwide.
7. Innovation and Future Trends
Challenge: Keeping Up with Technological Advances
The oil and gas industry is constantly evolving, with new technologies and methodologies emerging regularly. Manufacturers must stay ahead of these changes to maintain relevance and competitiveness.
Solution: Embracing Innovation
Investing in research and development (R&D) is critical to staying at the forefront of screen manufacturing. Areas of focus include:
- Intelligent Screens: Incorporating sensors and data analytics to monitor performance and predict maintenance needs.
- Sustainable Materials: Developing eco-friendly materials and processes to reduce environmental impact.
- Advanced Manufacturing Techniques: Exploring new technologies such as additive manufacturing (3D printing) for custom screen designs.
By embracing innovation, manufacturers can address future challenges and seize new opportunities in the oil and gas sector.
Overcoming the challenges in oil and gas screen manufacturing requires a multifaceted approach that includes advanced material selection, precision engineering, innovative designs, and effective cost management. By adopting these strategies and staying informed about industry trends and regulations, manufacturers can produce high-quality screens that meet the demanding needs of the oil and gas industry. As the industry continues to evolve, ongoing innovation and adaptation will be key to maintaining success and meeting the future challenges of oil and gas screen manufacturing.