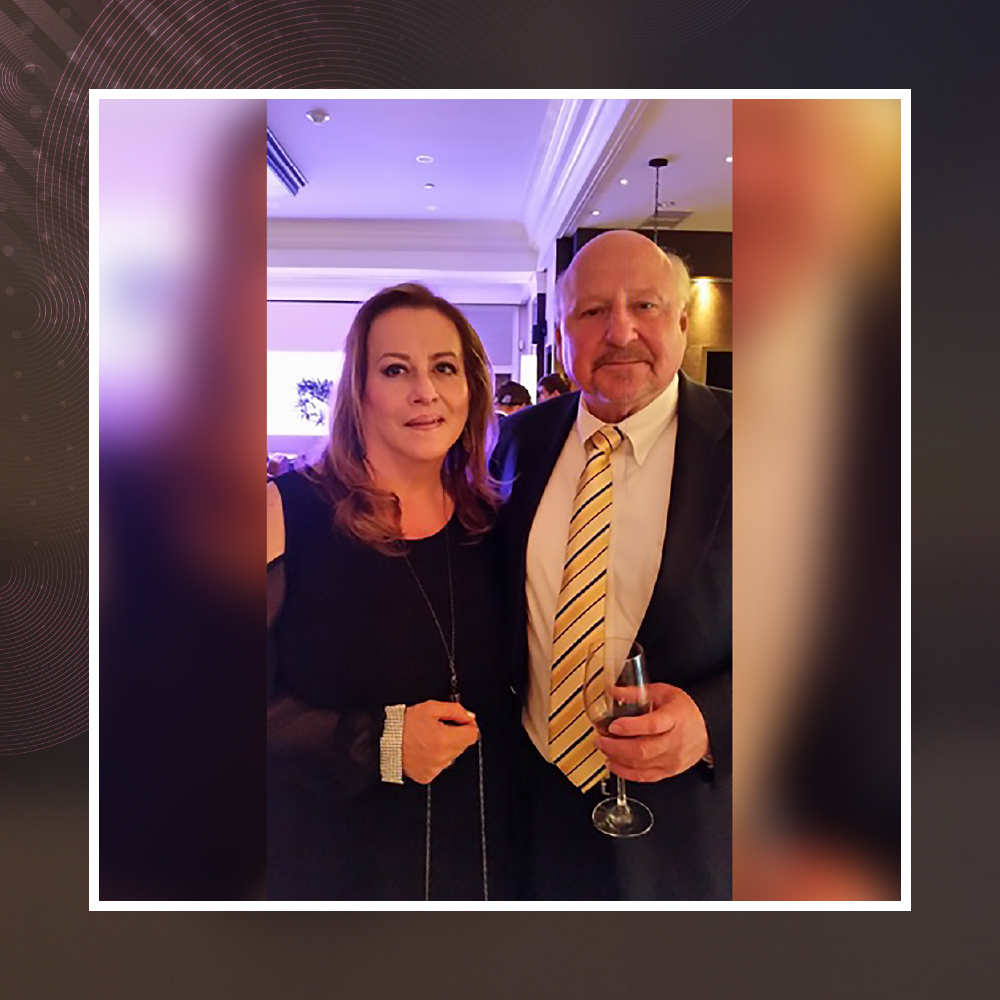
Oil and gas screens are crucial components in the petroleum industry, used to filter out debris and maintain the integrity of wells. Manufacturing these screens is a complex process fraught with numerous challenges, from material selection to quality control. Understanding these challenges is essential for improving manufacturing processes and ensuring the reliability and efficiency of oil and gas operations.
Material Selection and Durability
One of the primary challenges in oil and gas screen manufacturing is selecting materials that can withstand harsh operating conditions. Screens are often exposed to corrosive environments, including saltwater, acids, and hydrocarbons. Corrosion can significantly reduce the lifespan of a screen, leading to frequent replacements and increased operational costs. Manufacturers must carefully choose corrosion-resistant materials, such as stainless steel or specialized alloys, to ensure longevity and performance.
Oil and gas screens must also endure high pressures and mechanical stresses. The materials used need to provide sufficient mechanical strength to prevent deformation or failure during operation. This requirement adds another layer of complexity to the material selection process, as manufacturers must balance corrosion resistance with mechanical properties.
Manufacturing Precision and Tolerances
Achieving precise dimensions and tight tolerances is critical in oil and gas screen manufacturing. Even minor deviations can compromise the screen’s effectiveness, leading to operational issues such as improper filtration and equipment damage. Advanced manufacturing techniques, such as laser cutting and precision welding, are often employed to meet these stringent requirements. However, maintaining such high levels of precision can be challenging and requires continuous monitoring and quality control.
Consistency in manufacturing is another significant challenge. Each screen must meet the same high standards to ensure reliable performance. Variations in materials, manufacturing processes, or equipment settings can result in inconsistencies that affect screen quality. Implementing rigorous quality control measures and standardized procedures is essential to maintain consistency across production batches.
Quality Control and Testing
Quality control in oil and gas screen manufacturing often involves non-destructive testing (NDT) methods to identify defects without damaging the screens. Techniques such as ultrasonic testing, radiography, and magnetic particle inspection are used to detect flaws that could compromise performance. However, these methods can be costly and time-consuming, adding to the overall complexity of the manufacturing process.
In addition to NDT, performance testing is crucial to ensure that screens meet the required specifications. This testing includes evaluating the screen’s filtration efficiency, pressure drop, and mechanical strength. Conducting comprehensive performance tests on each screen can be challenging due to the time and resources required, but it is necessary to guarantee product reliability.
Technological Advancements and Integration
Automation is increasingly being integrated into oil and gas screen manufacturing to enhance efficiency and precision. Automated systems can perform repetitive tasks with high accuracy, reducing the potential for human error. However, integrating automation into existing manufacturing processes can be challenging, requiring significant investment and technical expertise.
The development of advanced materials, such as nanomaterials and composites, offers potential improvements in screen performance. These materials can provide enhanced corrosion resistance, mechanical strength, and filtration efficiency. However, incorporating advanced materials into manufacturing processes presents its own set of challenges, including compatibility with existing equipment and processes, as well as the need for specialized knowledge and skills.
Environmental and Regulatory Compliance
Manufacturing processes for oil and gas screens can produce emissions that must be controlled to comply with environmental regulations. Implementing effective emission control measures, such as scrubbers and filters, can be challenging and costly. Manufacturers must balance the need to minimize environmental impact with maintaining cost-effective production processes.
Waste management is another critical aspect of regulatory compliance. The manufacturing process can generate various types of waste, including metal shavings, chemical byproducts, and defective screens. Proper disposal and recycling of waste materials are essential to meet regulatory requirements and minimize environmental impact. Developing efficient waste management strategies can be complex and resource-intensive.
Supply Chain and Logistics
Securing a reliable supply of high-quality raw materials is essential for manufacturing oil and gas screens. Fluctuations in material availability or quality can disrupt production schedules and impact product quality. Establishing strong relationships with suppliers and diversifying sourcing options can help mitigate these risks, but it requires careful planning and coordination.
Oil and gas screen manufacturers often operate on a global scale, requiring efficient logistics to manage the distribution of products to customers worldwide. Challenges such as transportation delays, customs regulations, and geopolitical issues can impact the timely delivery of screens. Implementing robust logistics strategies and maintaining flexibility in supply chain operations are crucial to overcoming these challenges.
Cost Management
The complexity of oil and gas screen manufacturing results in high production costs. From material selection and precision manufacturing to quality control and compliance, each step of the process incurs significant expenses. Managing these costs while maintaining product quality and performance is a continuous challenge for manufacturers.
The oil and gas industry is highly competitive, with numerous manufacturers vying for market share. To remain competitive, manufacturers must continually innovate and improve their processes while controlling costs. This balancing act requires strategic investments in technology, workforce training, and process optimization.
Workforce and Expertise
Manufacturing oil and gas screens requires a skilled workforce with expertise in materials science, engineering, and precision manufacturing. Attracting and retaining skilled labor can be challenging, particularly in regions with a limited pool of qualified candidates. Investing in workforce development and training programs is essential to ensure the availability of skilled personnel.
As the manufacturing industry evolves, the transfer of knowledge and expertise from experienced workers to new generations becomes increasingly important. Implementing mentorship programs and comprehensive training initiatives can help preserve valuable knowledge and ensure that new employees are equipped with the skills needed to meet manufacturing challenges.
The manufacturing of oil and gas screens is a complex process that involves numerous challenges, from material selection and precision manufacturing to quality control and regulatory compliance. Addressing these challenges requires a combination of advanced technologies, skilled labor, and strategic planning. By understanding and overcoming these obstacles, manufacturers can enhance the performance, reliability, and cost-effectiveness of their products, ultimately contributing to the success of the oil and gas industry.