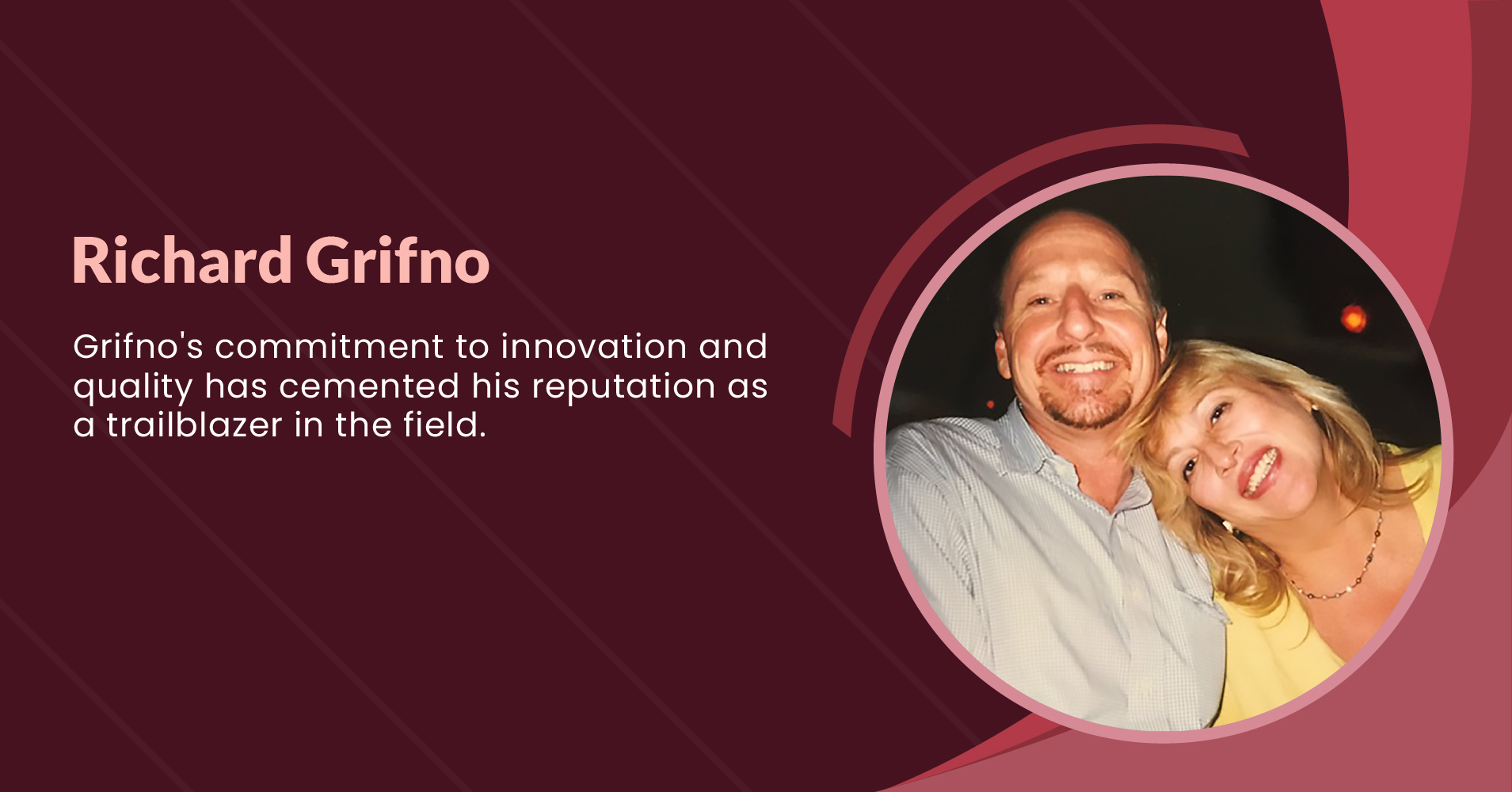
The oil and gas industry relies heavily on various equipment and technologies to extract, process, and transport hydrocarbons efficiently. Among these crucial components are screens used in oil and gas wells to filter out sand, debris, and other particles while allowing the flow of fluids. However, the manufacturing of these screens presents unique challenges that manufacturers must address to ensure quality, reliability, and safety in the field. In this article, we explore some of the key challenges faced in oil and gas screen manufacturing and the strategies employed to overcome them.
Material Selection and Compatibility
One of the primary challenges in oil and gas screen manufacturing is selecting materials that can withstand the harsh operating conditions encountered in good environments. These screens must be resistant to corrosion, erosion, high temperatures, and pressure fluctuations. Additionally, they need to be compatible with the fluids and chemicals present in the wellbore to prevent degradation or failure over time.
Manufacturers often utilize stainless steel alloys, such as 316L or 904L, due to their excellent corrosion resistance properties. These alloys offer superior resistance to corrosive fluids, including acids and chlorides, commonly found in oil and gas wells. Titanium and nickel-based alloys are also employed in applications where extreme corrosion resistance is required. However, selecting the appropriate material involves careful consideration of factors such as temperature, pressure, fluid composition, and mechanical stress to ensure optimal performance and longevity of the screens.
Precision Manufacturing and Quality Control
Oil and gas screens are intricate components with precise specifications to ensure effective filtration and fluid flow. Manufacturing these screens requires advanced machining techniques, such as laser cutting, welding, and perforating, to achieve the desired dimensions, perforation patterns, and surface finishes. Any deviation from the specified tolerances can compromise the performance and integrity of the screens, leading to reduced efficiency and potential equipment failure in the field.
To maintain quality and consistency, manufacturers implement stringent quality control measures throughout the manufacturing process. This includes inspection of raw materials, in-process monitoring, and final product testing to verify dimensional accuracy, mechanical properties, and corrosion resistance. Advanced imaging technologies, such as optical and scanning electron microscopy, are employed to examine microstructural features and detect any defects or anomalies that may affect the performance of the screens.
Customization and Flexibility
Oil and gas wells vary greatly in terms of depth, formation characteristics, fluid composition, and production rates, requiring customized solutions to meet specific operational requirements. Manufacturers must be able to tailor the design, size, and configuration of screens to accommodate these diverse conditions while ensuring optimal performance and reliability.
Advanced modeling and simulation techniques, such as computational fluid dynamics (CFD) and finite element analysis (FEA), are utilize to optimize the design and performance of screens for different well conditions. This allows manufacturers to predict fluid flow behavior, pressure drop, erosion rates, and other critical parameters, enabling them to design screens that maximize productivity and minimize operational risks.
Environmental and Regulatory Compliance
The oil and gas industry is subject to stringent environmental regulations aimed at protecting air, water, and land resources from pollution and contamination. Manufacturers of oil and gas screens must comply with various environmental standards and regulations governing the use of materials, emissions, waste management, and disposal practices.
This includes adherence to international standards such as ISO 9001 for quality management systems and ISO 14001 for environmental management systems. Additionally, manufacturers must ensure that their products meet industry-specific standards and certifications, such as API Spec 5CT for casing and tubing, API RP 19C for sand control screens, and NACE MR0175 for materials compatibility in sour gas environments.
Supply Chain Management and Logistics
The global nature of the oil and gas industry presents challenges in terms of supply chain management, sourcing of raw materials, and logistics. Manufacturers must navigate complex supply chains involving multiple suppliers, subcontractors, and distributors to procure raw materials, components, and equipment required for screen manufacturing.
Disruptions in the supply chain, such as shortages, price fluctuations, or geopolitical instability, can impact production schedules and lead to delays in delivering screens to customers. To mitigate these risks, manufacturers often maintain strategic partnerships with reliable suppliers, implement inventory management systems, and diversify sourcing sources to ensure continuity of supply.
The manufacturing of oil and gas screens is a complex and demanding process that requires careful consideration of material selection, precision manufacturing, customization, environmental compliance, and supply chain management. By addressing these challenges effectively, manufacturers can deliver high-quality screens that enhance the performance, reliability, and safety of oil and gas operations, ultimately contributing to the efficiency and sustainability of the industry.